IV Fluid Manufacturing Plant
Home / IV Fluid Manufacturing Plant
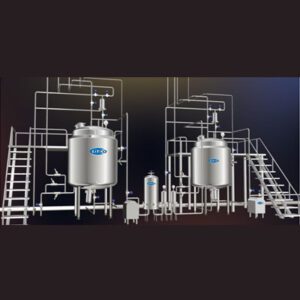
Intravenous Fluid or IV Fluid has quickly become one of the most in-demand and important drugs in hospitals for critical care patients. This Parenteral Drug is one of the widely administered fluids globally, whose formulation and production is a significant and critical process. LITCOMachinery with their immense experience and expertise in designing Sterile Manufacturing plants,has established themselves as one of the leading designers and manufacturers of IV Fluid Manufacturing Plant as we make customizedplants.
IV Fluids which are provided directly to patients, means important aspects need to be maintained during the production process. Commonly provided IV Fluids are Saline and Dextrose. From other Pharmaceutical products, parenteral dosage such as IV Fluid need to fulfill various criteria before they can be administered:-
- Product must be complete sterile
- Product must be physically, chemically and micro-biologically stable throughout its life
- Free from any contamination such as pyrogens
Aseptic Conditions during production is of utmost importance as contamination of processing product has to be prevented. Many Pharmaceutical products are highly reactive and volatile hence it is of utmost important to produce them in Aseptic Conditions that will not contaminate the product. LITCO has mastered the best practices in Industry to provide the best sterile, secured and highly productive plant for Aseptic production. Automation is of utmost importance in Sterile Production and LITCO offers the best automotive process and instrumentation with almost no manual handling of the material.
LITCO’s standard IV Fluid Manufacturing Plant consists of the following:
- Sterile Mixing Vessel( Magentic / Mixing Anchor)
- Sterile Storage Vessel
- Powder Feeding System
- In-line Homogenizer
- Membrane Filter
- Cartridge Filter
- Vacuum System for Online Transfer
- Plant Pipeline
- Aseptic Valves
- Automated Control Panel
WORKING PRINCIPLE OF IV FLUID MFG. PLANT
IV Fluid Manufacturing plant requires absolute sterile conditions for processing hence it is designed to produce aseptic environment with automated processes, to ensure minimal contact. The IV Fluid being a Sterile product follows the basic of other Sterile Manufacturing plants. Sterile Mixing Vessels are provided with Mechanical/Magnetic Stirrer. The Magnetic Stirrer is most recommended to ensure least contamination and contact. Depending upon the nature of process, provision for powder feeding system is also provided into the Sterile Mixing Vessels.
The product is then passed through an In-line Homogenizer for further mixing. Then it is made to pass through a series of Filters such as the Membrane or Cartridge Filter depending upon the user’s requirement. The entire transfer is handled by an Online Vacuum Transfer system for the best productivity and ease of use.
Another important aspect in Sterile Mfg. Plants is to ensure no Dead Legs to prevent unwanted microbial growth. Hence Zero Dead Leg Valves with other Aseptic Valves are provided according to the plant design to prevent impurity formation. The produced Sterile solution is finally transferred to the Sterile Storage Vessel which is then carried forward for packaging or other processes. The entire process is undertaken by our smart Automated Control System with an easy-to-use HMI ensuring all the processes are completed on-time, efficiently and hassle-free with no manual handling.
At LITCO, we manufacture IV Fluid Manufacturing Plant and IV Fluid Packaging Machinery as per our Customer’s requirements. We specialise in providing our Client’s customised Plant design and Turnkey solutions. Please drop in your requirements under our Contacts for further specifications and quotations.
special FEATURES:
- Complete aseptic design with Magnetic mixer & high shear Magnetic emulsifier.
- Zero dead leg aseptic design Flush bottom outlet diaphragm valve with SIP facility.
- Sampling valve zero dead leg type with CIP/SIP facility.
- Volume monitoring by Load Cell for accurate measurement and result.
- PH Sensor / Conductivity Sensor provided on demand for online check Product PH & Conductivity.
- The gaskets used are of Silicon (food grade) to avoid contamination
- Mechanical Seal is provided at the Stirrer Entry to prevent back-flow and contamination.
- All material transfers are done by vacuum hence assuring minimal contact.
- All the Vessels are CGMP standard (paint free construction).
- All contact parts are made of SS 316 grade and non-contact parts SS 304.
- All pipelines are joined with Tri-clover ended Joints assuring safe and smooth transport.
- PLC with HMI Touchscreen with CFR 21 Part 11 complied with SCADA for fully Automatic Control & Processing.
TECHNICAL SPECIFICATIONS | |||||||
MODEL | LIVPRO-50 | LIVPRO-100 | LIVPRO-500 | LIVPRO-1000 | LIVPRO-2000 | LIVPRO-5000 | LIVPRO-10000 |
Capacity | 50 Litres. | 100 Litres. | 500 Litres. | 1000 Litres. | 2000 Litres. | 5000 Litres. | 10000 Litres. |
Gross Capacity | 60 Litres. | 120 Litres. | 600 Litres. | 1200 Litres. | 2400 Litres. | 6000 Litres. | 12000 Litres. |
MOC |
·All Contact Parts SS316 ·All Non-Contact Parts SS304 |
·All Contact Parts SS316 ·All Non-Contact Parts SS304 |
·All Contact Parts SS316 ·All Non-Contact Parts SS304 |
·All Contact Parts SS316 ·All Non-Contact Parts SS304 |
·All Contact Parts SS316 All Non-Contact Parts SS304 |
·All Contact Parts SS316 All Non-Contact Parts SS304 |
·All Contact Parts SS316 All Non-Contact Parts SS304 |
Jacket Material | Water | Water | Water | Water | Water | Water | Water |
Heating Element | Electrical/Steam Heater | Electrical/Steam Heater | Electrical/Steam Heater | Electrical/Steam Heater | Electrical/Steam Heater | Electrical/Steam Heater | Electrical/Steam Heater |
Material of Insulation | Glass Wool | Glass Wool | Glass Wool | Glass Wool | Glass Wool | Glass Wool | Glass Wool |
Agitator Type | Magnetic/Mechanical | Magnetic/Mechanical | Magnetic/Mechanical | Magnetic/Mechanical | Magnetic/Mechanical | Magnetic/Mechanical | Magnetic/Mechanical |
Insulation | 50 MM | 50 MM | 50 MM | 50 MM | 50 MM | 50 MM | 50 MM |
Agitator Location | Top/ Bottom Fixed Stirrer | Top/ Bottom Fixed Stirrer | Top/ Bottom Fixed Stirrer | Top/ Bottom Fixed Stirrer | Top/ Bottom Fixed Stirrer | Top/ Bottom Fixed Stirrer | Top/ Bottom Fixed Stirrer |
Motor |
1 HP, 50-960 RPM, TEFC, ISI make motor | 1 HP, 50-960 RPM, TEFC, ISI make motor | 3 HP, 50-960 RPM, TEFC, ISI make motor | 5 HP, 50-960 RPM, TEFC, ISI make motor | 7.5/10 HP, 50-960 RPM, TEFC, ISI make motor | 15 HP, 50-960 RPM, TEFC, ISI make motor | 30 HP, 50-960 RPM, TEFC, ISI make motor |
Power Supply | 415 V / 50 Hz/3 Ph/AC | 415 V / 50 Hz/3 Ph/AC | 415 V / 50 Hz/3 Ph/AC | 415 V / 50 Hz/3 Ph/AC | 415 V / 50 Hz/3 Ph/AC | 415 V / 50 Hz/3 Ph/AC | 415 V / 50 Hz/3 Ph/AC |
LITCO manufactures Customised Injectable/Sterile Processing & Packaging Plant as per Customer’s requirements apart from these Standard Models. |